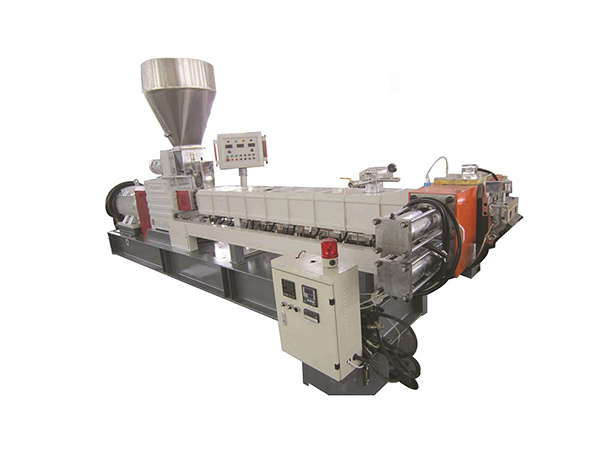
Tipping bucket internal mixers are specialized machines used primarily in the construction and building materials industry for the efficient mixing of various materials. These mixers have gained popularity due to their ability to provide homogeneous mixtures, save time, and reduce labor costs. Understanding the features, advantages, and applications of tipping bucket internal Tipping Bucket Internal Mixer can help businesses in making informed decisions about their mixing needs.
1. Design and Operation
The tipping bucket internal mixer consists of a robust and well-engineered design that allows for effective mixing of both dry and wet materials. The internal structure typically features a series of mixing blades that rotate within a sealed chamber. As the materials are added, these blades agitate the mixture thoroughly. The “tipping bucket” component refers to the system that allows for easy discharge of the mixed materials, often achieved by tilting the mixing chamber.
2. Key Features
One of the defining characteristics of tipping bucket internal mixers is their ability to operate under high shear conditions, making them ideal for materials that require a fine and uniform blend. These mixers are equipped with variable speed settings, enabling users to adjust the mixing intensity according to the specific requirements of different materials. Additionally, many models incorporate automated controls and sensors for monitoring consistency and quality, ensuring that the final product meets desired specifications.
3. Advantages of Tipping Bucket Internal Mixers
- Efficiency: The tipping bucket design facilitates quick loading and unloading, significantly reducing the time spent on mixing processes.
- Homogeneity: The high shear mixing action ensures that materials are thoroughly blended, which is crucial for applications requiring precise formulations, such as in concrete production.
- Versatility: These mixers can handle a wide variety of materials, including aggregates, cement, polymers, and various additives, making them suitable for multiple industries.
- Reduced Labor Costs: Automated features reduce the need for manual intervention, which can lower labor costs and improve overall productivity.
4. Applications
Tipping bucket internal mixers are widely used in various sectors, including:
- Construction: For producing concrete and mortar mixtures with precise specifications.
- Chemical Industry: In the formulation of adhesives, sealants, and coatings where a consistent mixture is essential.
- Food Processing: For mixing ingredients in the production of certain food items, ensuring that flavors and textures are uniformly distributed.
- Pharmaceuticals: For creating homogeneous mixtures of active pharmaceutical ingredients (APIs) and excipients.
5. Maintenance and Care
To ensure longevity and optimal performance, regular maintenance of tipping bucket internal mixers is essential. This includes routine inspections of the mixing blades for wear and tear, cleaning of the mixing chamber to prevent cross-contamination of materials, and checking all electrical components to ensure they are functioning correctly. Following the manufacturer’s maintenance schedule can help avoid costly repairs and downtime.
6. Choosing the Right Mixer
When selecting a tipping bucket internal mixer, several factors should be considered, including the type of materials to be mixed, the required batch size, and the desired mixing speed. It is also beneficial to look for models that offer scalability, allowing businesses to adjust production capacities as demand fluctuates. Consulting with manufacturers or industry experts can provide insights into the best mixer for specific applications.
7. Future Trends
As industries continue to evolve, the design and functionality of tipping bucket internal mixers are also advancing. Innovations such as smart technology integration, where mixers are equipped with IoT sensors for real-time monitoring, are becoming more prevalent. These advancements not only enhance the efficiency of mixing processes but also allow for better quality control and data analysis, paving the way for improved production processes in various industries.
8. Conclusion
Tipping bucket internal mixers represent a significant advancement in material mixing technology. Their efficient design, coupled with the ability to produce uniform mixtures across a range of materials, makes them an invaluable asset in industries where quality and consistency are paramount. By understanding their features, applications, and maintenance needs, businesses can effectively leverage these mixers to enhance productivity and improve product quality.
9. Case Studies
Real-world applications of tipping bucket internal mixers highlight their effectiveness. For instance, a leading construction company reported a 30% increase in production efficiency after integrating a tipping bucket mixer into their concrete batching process. Similarly, a chemical manufacturer noted improved product consistency and reduced waste, contributing to overall cost savings. These case studies exemplify how adopting advanced mixing technologies can drive operational improvements.
10. Final Thoughts
In conclusion, tipping bucket internal mixers play a critical role in modern manufacturing and construction processes. As industries continue to seek ways to optimize operations and improve product quality, investing in efficient mixing solutions like tipping bucket internal mixers can yield significant long-term benefits. As technology advances, these mixers will likely incorporate even more innovative features, making them essential tools in various sectors.